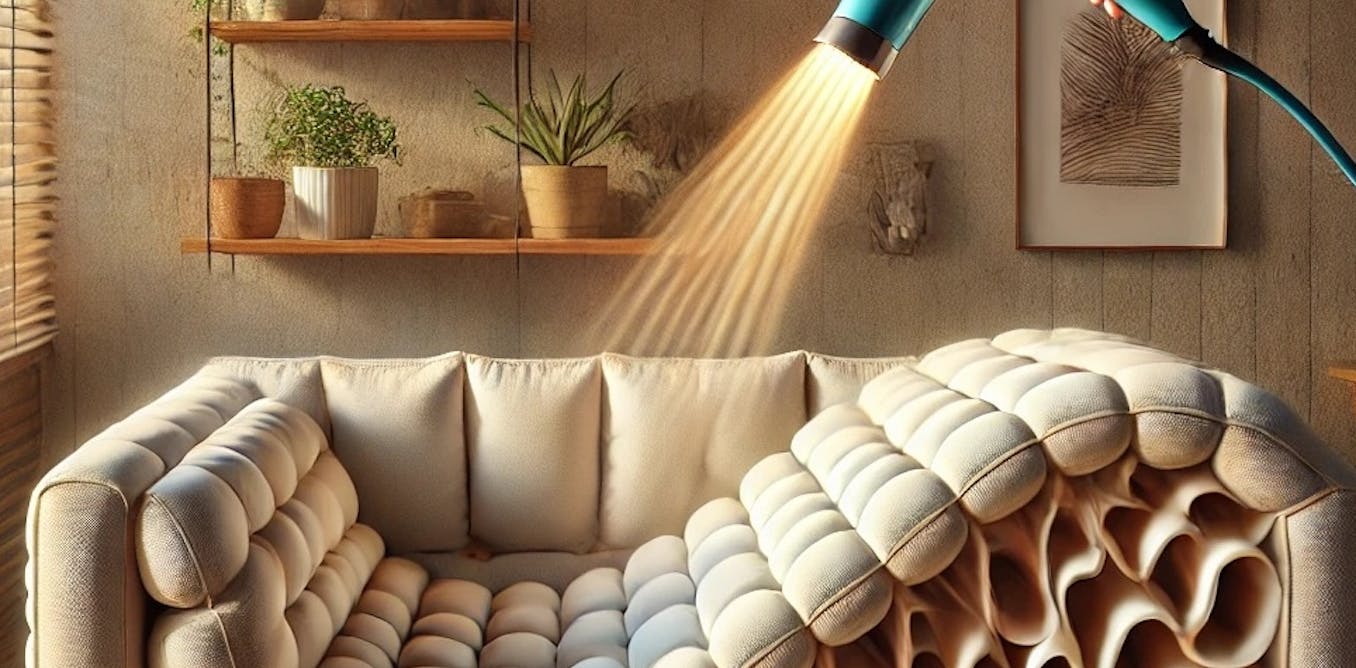
Picture purchasing a flat piece of material from a store that transforms into a sofa when warmed with a hairdryer. Or think about the significance of a stent that expands precisely within a patient’s artery, adjusting to their individual anatomy.
Welcome to the realm of 4D printing, an exciting and rapidly evolving area of materials science and manufacturing that has gained momentum in the past ten years. While 3D printing has garnered considerable attention for its ability to construct objects layer by layer, 4D printing introduces the crucial factor of time.
This innovative process entails 3D-printing adaptable objects from materials like polymers or alloys that can bend, twist, or completely alter their form when subjected to heat or moisture. By moving beyond still designs, it paves the way for extraordinary applications in diverse fields including healthcare, aerospace, robotics, and construction.
Recently, I had the privilege of being the lead author on a detailed report published in the journal Smart Materials and Structures, detailing the advancements and hurdles within this domain. We highlighted the immense potential of this industry, envisioning a future where intelligent materials revolutionize design and manufacturing.
Here are some key sectors where 4D printing could bring significant changes:
1. Healthcare
As mentioned with the stent, 4D printing holds the potential to develop implants and prosthetics that adjust in real-time to the requirements of patients. Research teams such as the Biomet4D project, led by the IMDEA Materials Institute in Madrid, are working on intelligent, biodegradable metallic implants for individuals with severely damaged or malformed bones. These implants can morph and expand as the bone develops, offering more effective support than a conventional implant.
Another promising aspect is the smarter administration of medications. For instance, researchers at Jilin University in China have developed 4D-printed hydrogel capsules that maintain their outer structure inside the patient’s body until a specific temperature is achieved, such as during an infection. This means the medication activates only when truly needed, which is especially beneficial for targeted drug delivery.
2. Robotics and Wearables
Incorporating 4D materials into robotics and wearable technology enables these devices to modify their functions based on environmental conditions. For example, researchers at Harvard University’s Wyss Institute are developing self-folding robotic systems inspired by origami, which change shape when exposed to heat. These devices could be deployed in challenging environments, such as deep underwater.
Similarly, scientists at Deakin University in Australia are exploring 4D-printed robotic joints with adjustable stiffness that can assist in rehabilitation. For instance, an arm could increase in stiffness when a user attempts to lift an object, making the task more manageable.
3. Space Exploration
In the harsh conditions of outer space, adaptability is vital, which is where 4D-printed materials come into play. For example, NASA’s Jet Propulsion Laboratory utilizes 4D-printed metallic fabrics designed for space applications.
These materials can fold, change form, and adjust to different thermal and mechanical environments. Their versatility makes them suitable for a range of space applications, from shielding spacecraft against meteoroids to insulating against extreme temperatures and adapting to the uneven surface of Europa, one of Jupiter’s moons.
Challenges and Opportunities
While the current capabilities of 4D printing are impressive, the technology still faces substantial challenges. Although we can now create materials that transform with remarkable accuracy, further research is necessary to guarantee their biological safety and long-term durability.
Additionally, increasing production to meet industrial needs, especially for high-resolution designs or nanoscale structures, demands not only new techniques but also innovative perspectives on manufacturing. Cost remains another hurdle; specialized materials and processes are often prohibitively expensive for widespread implementation.
However, the potential of 4D printing is incredibly enticing. One of its major draws is sustainability. From water pipes that regulate flow rates to buildings that spontaneously adjust their carbon dioxide levels, 4D printing opens avenues for adaptive systems that contribute to environmental preservation. A prominent example is the Solar Gate, created by the University of Stuttgart’s Institute for Computational Design and Construction.
Inspired by how pine cones react to sunlight, the Solar Gate features a series of 4D-printed cellulose flaps that can be integrated into buildings to open and close based on specific humidity and temperature levels. They curl up in winter to let warmth in and lay flat in summer to block direct sunlight, illustrating how buildings can enhance energy efficiency without relying on external power sources like air conditioning.
Moreover, artificial intelligence is currently propelling advancements by optimizing the design and performance of 4D-printed materials. AI enables researchers to achieve more accurate control over how these smart materials behave in different environments, minimizing reliance on trial and error.
This is still an emerging industry, characterized by limited venture capital investment and a workforce that is just beginning to develop. However, as more research institutions and companies see the promise in this technology, the rate of innovation is expected to accelerate. According to recent reports, the sector is anticipated to experience a growth rate of approximately 35% annually over the next five years.
At the 4D materials and printing laboratory at Nottingham Trent University and the 4D Printing Society, we are actively working on structures that can revert or alter their shapes on demand. For example, we have successfully produced 4D-printed medical stents that self-expand in response to body temperature (see images below).
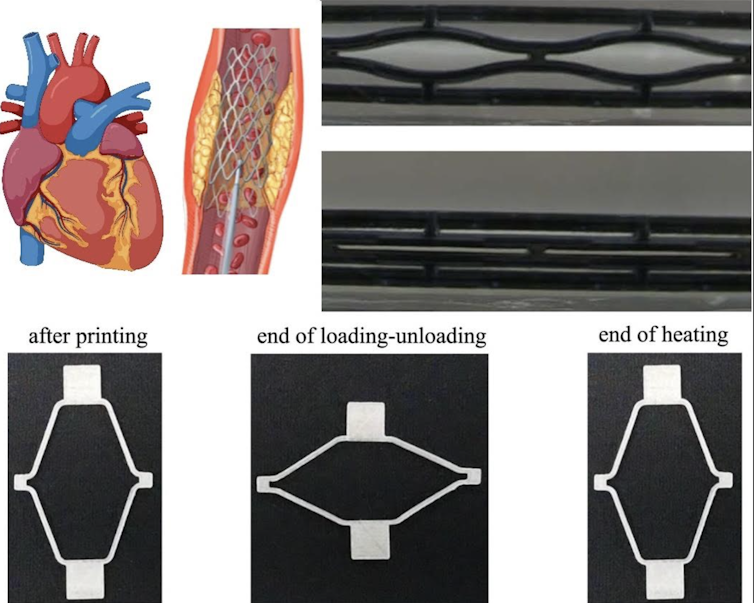
Nottingham Trent University, CC BY-SA
Additionally, we are creating materials for boat fenders and car bumpers that can regain their shape when heated, effectively eliminating dents, as well as shape-adaptive finger splints for fractures, and self-assembling, highly comfortable furniture.
So next time you are amazed by the capabilities of 3D printing, keep in mind: the future lies in 4D printing, where materials take on new life and broaden the horizons of what is possible.
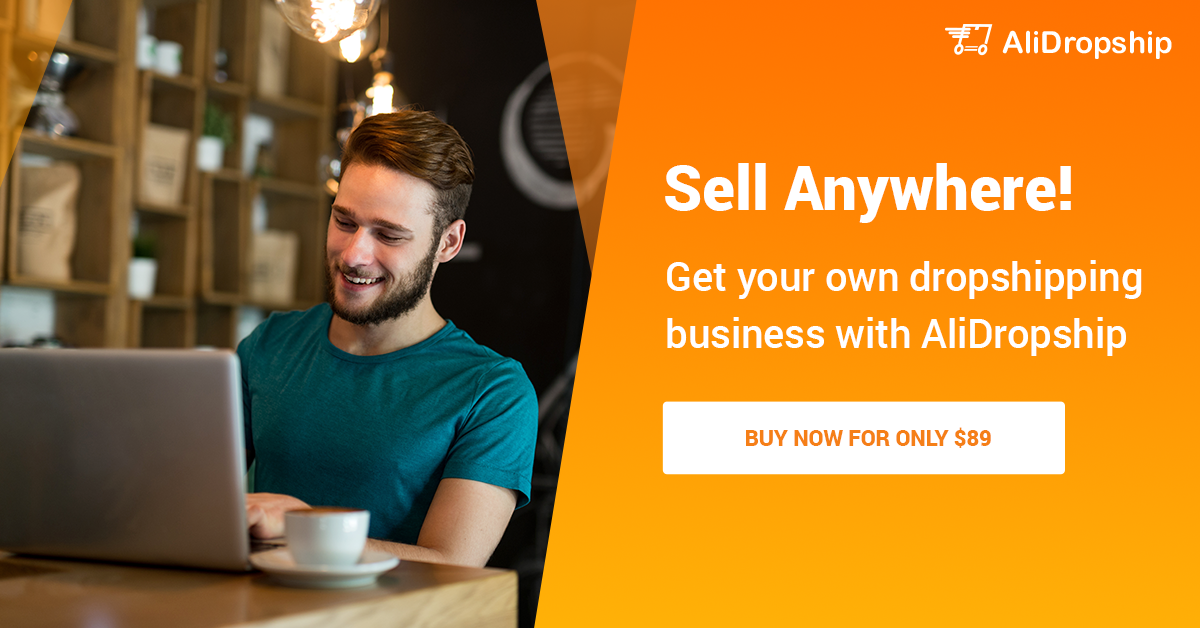