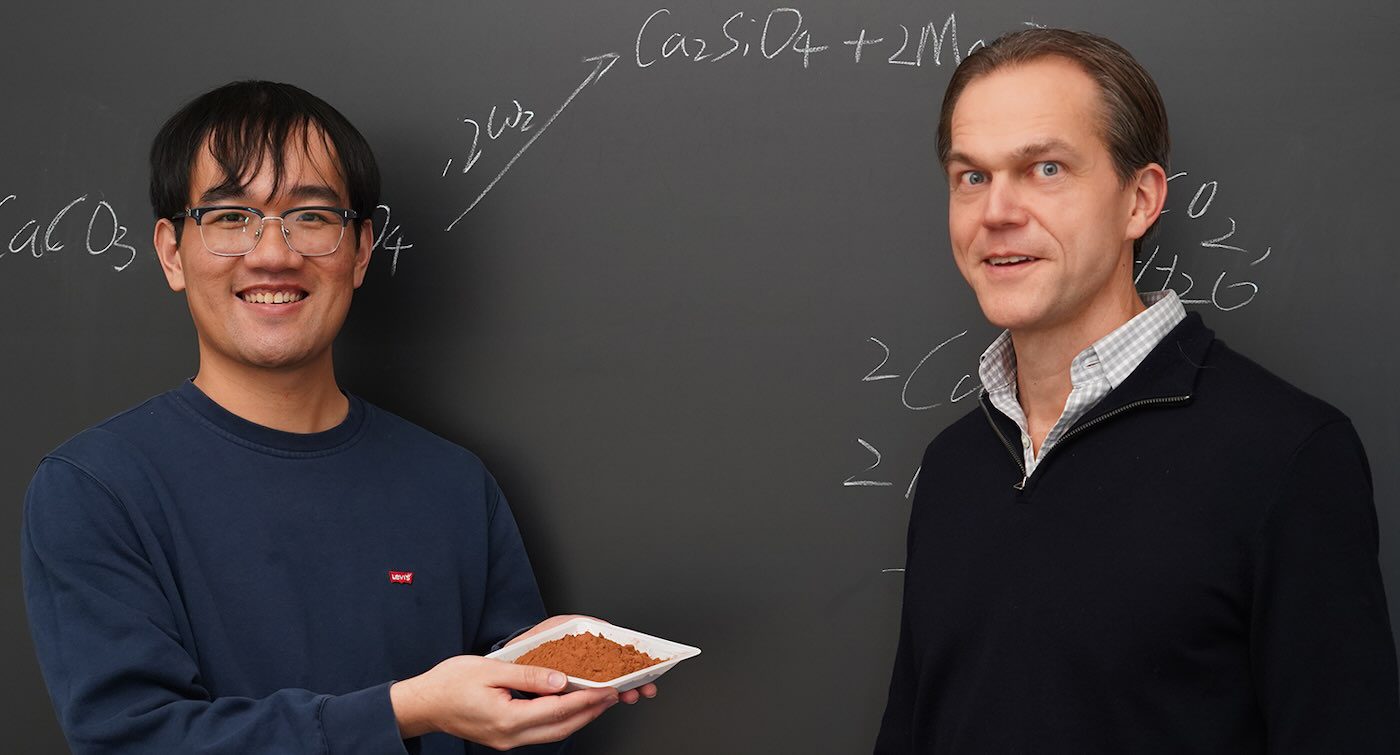
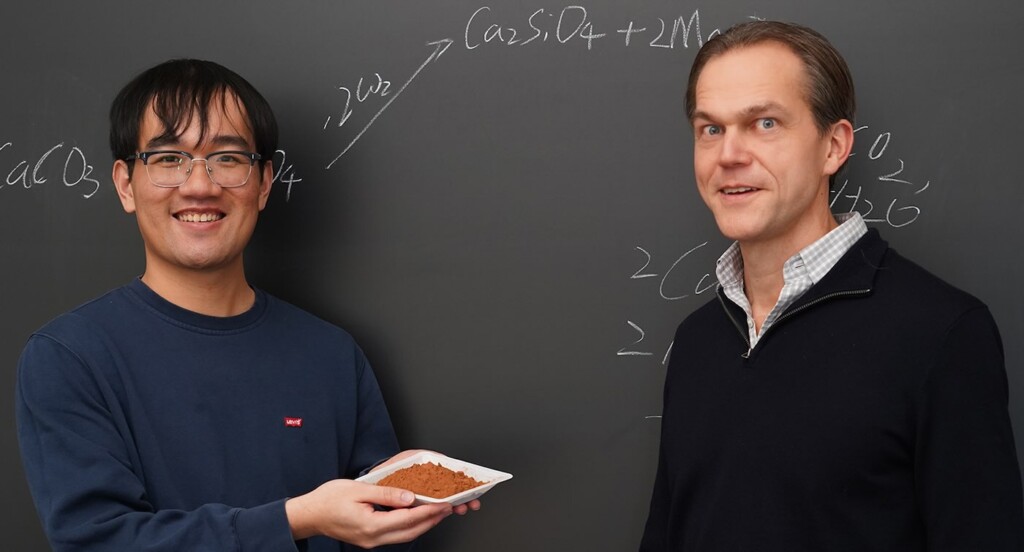
Researchers from Stanford University have unveiled an innovative and cost-effective solution for permanently eliminating carbon dioxide from the atmosphere, a primary contributor to climate change and global warming.
This groundbreaking method utilizes heat to convert ordinary minerals into substances that naturally capture carbon from the air and sequester it indefinitely. These active materials can be manufactured using conventional kilns, similar to those employed in cement production.
“Earth possesses an endless supply of minerals that can eliminate CO2, but they lack the necessary reactivity to make a significant impact against human emissions,” explains Matthew Kanan, a Stanford chemistry professor and senior author of a recent study published in Nature. “Our research addresses this challenge with a scalable solution.”
In the natural world, silicate minerals react with water and atmospheric CO2 to generate stable bicarbonate ions and solid carbonate minerals, a phenomenon known as weathering. However, this reaction traditionally takes hundreds to thousands of years. Since the 1990s, scientists have sought to accelerate this process to enhance the absorption of carbon dioxide.
Kanan, along with postdoctoral researcher Yuxuan Chen, has pioneered a technique to transform slow-reacting silicates into highly reactive minerals that can effectively capture carbon from the atmosphere.
“Our goal was to activate these dormant silicate minerals through a straightforward ion-exchange reaction,” Chen elaborated. “The results exceeded our expectations.”
Carbon capture technologies have the potential to mitigate further global warming, but existing methods are often expensive and energy-intensive. These typically involve using large fans or panels to pull air through various chemical processes to extract CO2.
“Our method consumes less than half the energy of current direct air capture technologies and can be competitively priced,” Kanan asserts.
Inspired by Traditional Cement Production Techniques
The manufacture of cement begins with heating limestone to form calcium oxide in a kiln at approximately 1,400 degrees Celsius. This calcium oxide is then combined with sand to create a vital component of cement.
The Stanford team employed a similar approach, substituting sand with calcium oxide and another mineral rich in magnesium and silicate ions. Upon heating, these minerals exchanged ions, resulting in magnesium oxide and calcium silicate—two alkaline minerals that quickly react with acidic CO2 found in the atmosphere.
In preliminary reactivity tests at room temperature, the calcium silicate and magnesium oxide were exposed to both water and pure CO2, leading to a total transformation into new carbonate minerals within just two hours, locking in the carbon from CO2.
Conducting a more authentic assessment, wet samples of calcium silicate and magnesium oxide were exposed to ambient air, which contains significantly lower concentrations of CO2 than pure CO2 sources. This carbonation process occurred over weeks to months, still thousands of times faster than natural weathering.
Environmental Benefits for Agriculture
“Imagine applying magnesium oxide and calcium silicate across expansive land to capture CO2 from the atmosphere,” Kanan proposed. “We are currently exploring an exciting application of adding these minerals to agricultural soil. As they weather, they convert into bicarbonates, which can permeate the soil and eventually be sequestered in the ocean.”
Kanan noted that this approach could provide additional benefits for farmers, who often apply calcium carbonate to adjust soil pH—a process known as liming.
“Incorporating our products would replace the need for liming, as both minerals are alkaline,” he clarified.
“Moreover, as calcium silicate weathers, it releases silicon in a bioavailable form for plants, enhancing crop yields and resilience. Ideally, farmers would invest in these minerals for their agricultural benefits, with the added advantage of capturing carbon.”
Utilizing Mining Byproducts on a Global Scale
Currently, Kanan’s lab can produce 15 kilograms (33 pounds) of this innovative material weekly, but kilns designed for cement production could easily scale up to manufacture the necessary quantities for effective CO2 removal. Abundant sources of magnesium silicates, such as olivine and serpentine, can be found in California, the Balkans, and various other locations. These materials often constitute leftover tailings from mining operations.
“Over 400 million tons of suitable mine tailings are produced annually worldwide, creating a significant potential resource,” Chen noted. “It is estimated that more than 100,000 gigatons of olivine and serpentine reserves exist on Earth, enough to sequester far greater amounts of CO2 than humanity has ever emitted.” (One gigaton equates to 1 billion metric tons or approximately 1.1 billion tons.)
Explore More Carbon Capture Innovations:
• New Wyoming Carbon Capture Initiative Aims for 5 Million Tons of CO2 Reduction Annually
• UK’s Largest Carbon Capture Initiative Converts 40,000 Tons of CO2 into Baking Soda
• Significant Growth in Carbon Capture Projects Reflects Global Commitment to Emission Reductions
After factoring in the emissions generated from burning natural gas or biofuels to power the kilns, the research team estimates that each ton of reactive material could extract one ton of carbon dioxide from the atmosphere.
The researchers are also working on kilns powered by electricity instead of fossil fuels, supported by a grant that is propelling the transition from research to practical application.
(Original Source: Stanford Report) – SHARE THIS BREAKTHROUGH ON SOCIAL MEDIA!
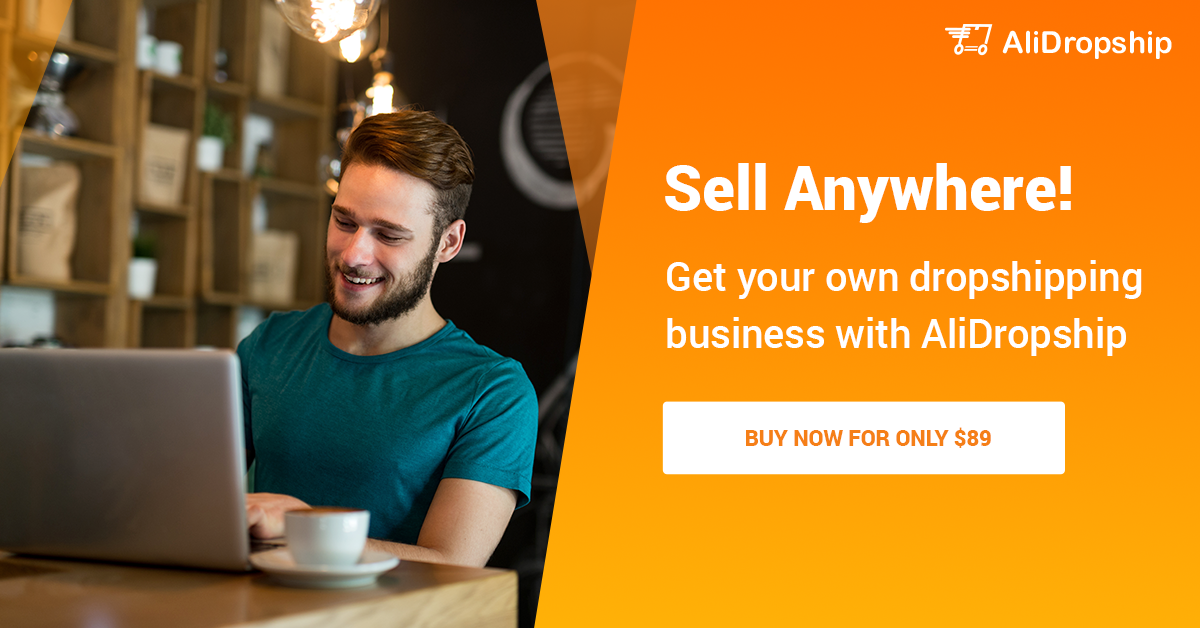